Computer-Controlled Machining
Computer-controlled machining, also known as CNC (computer numerical control) machining, is a manufacturing process that uses computers to control machine tools. CNC machines can perform precise and complex operations on materials such as metal, plastic, and wood.
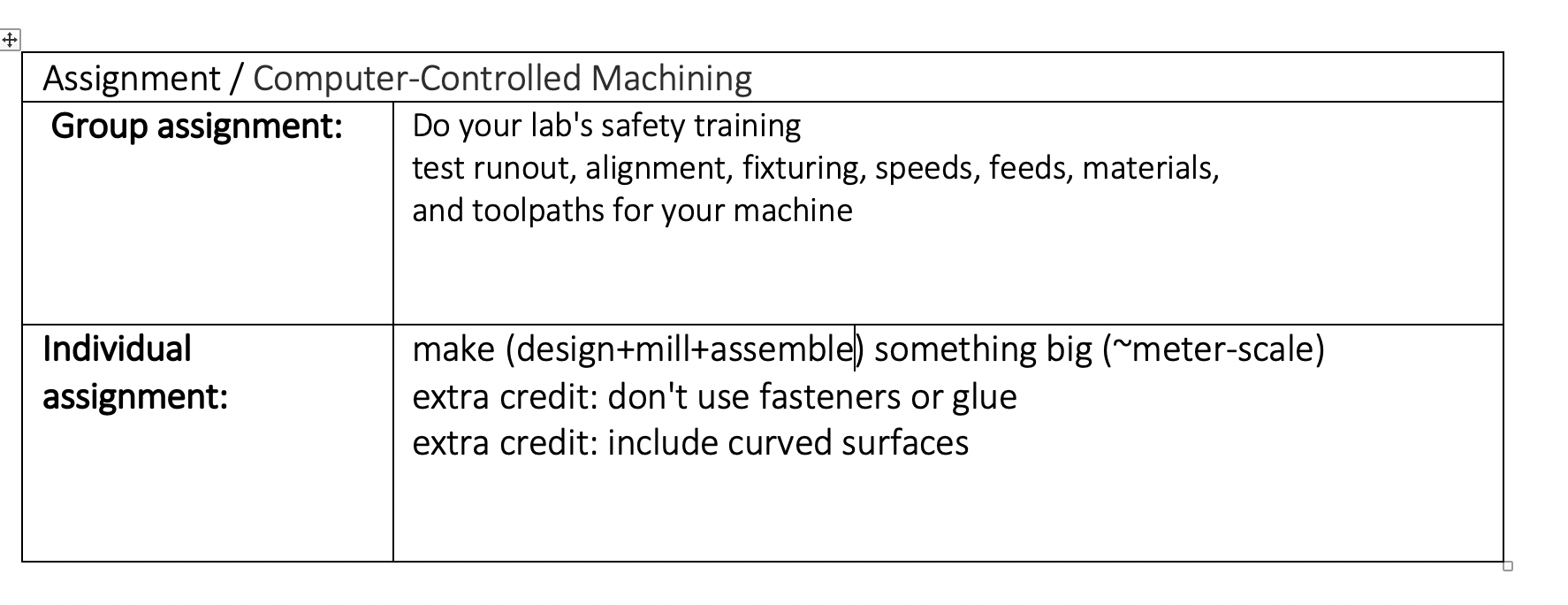
Group Assignment
Design of Pavilion
1. Safety in the Lab
Before getting involved in working with the CNC machine, it was necessary to review safety criteria. For this, it was necessary to use the right equipment: goggles, gloves, and dust masks. It was also important to learn about emergency procedures and how to handle the tools correctly.
2. Preparation: Eccentricity, Alignment, and Clamping
In principle, what was expected was the most precise cuts possible, so we started by checking the eccentricity of the machine. Using a dial indicator, we made sure everything was within 0.01 mm of perfect. We carefully lined up our 9mm plywood on the workbench, tightening it with stops and clamps to ensure it wouldn't move. This step saved us frustration later.
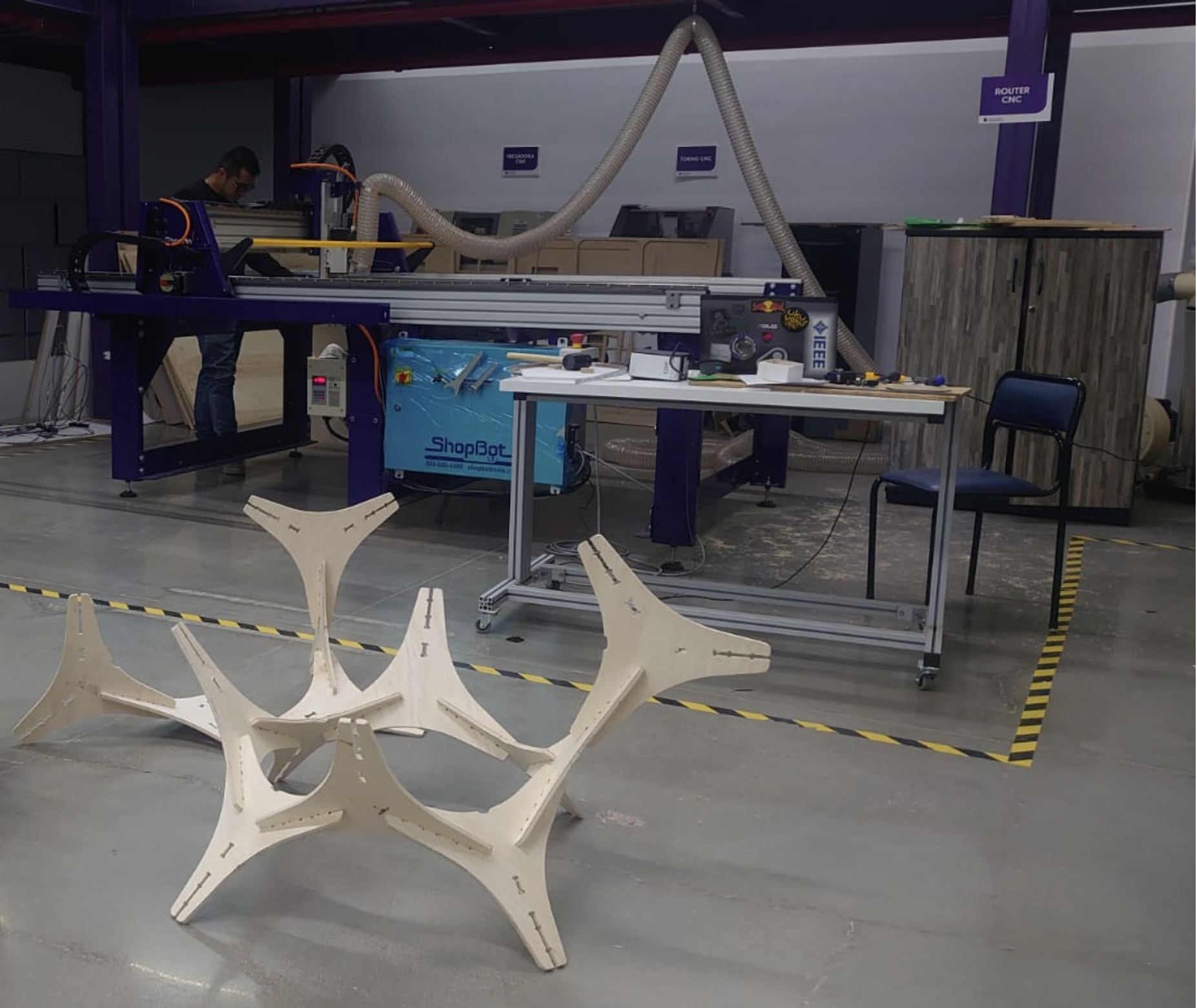
3. The Neatest Cut: Speeds, Feeds, and Trajectories
Now we need to set up the machine, so we chose a 6 mm straight cutter and programmed our speeds and feeds:
- Spindle speed: 12,000 RPM
- Feed rate: 2000 mm/min
- Depth per pass: 3 mm
- Pitch per pass: 50% of tool diameter
- Cutting direction: Rising milling for smoother results
4. Designing and Building Something Impressive
We tested different joint designs:
- Standard Fit: Simple cut to test the fit of the parts.
- Press-Fit with Teeth: This one had small interlocking notches for extra grip.
- Anchored Joint: We added an additional locking system for a stronger joint.
- Reinforced Press-Fit Joint: An additional channel and teeth make this the most secure.
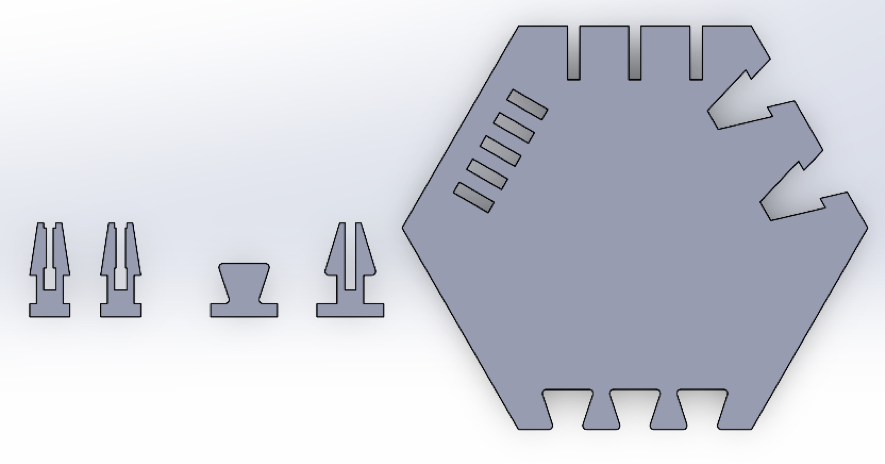
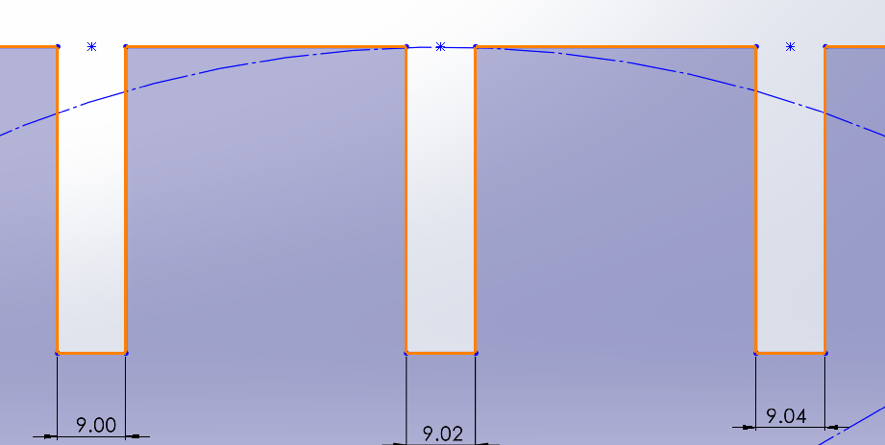
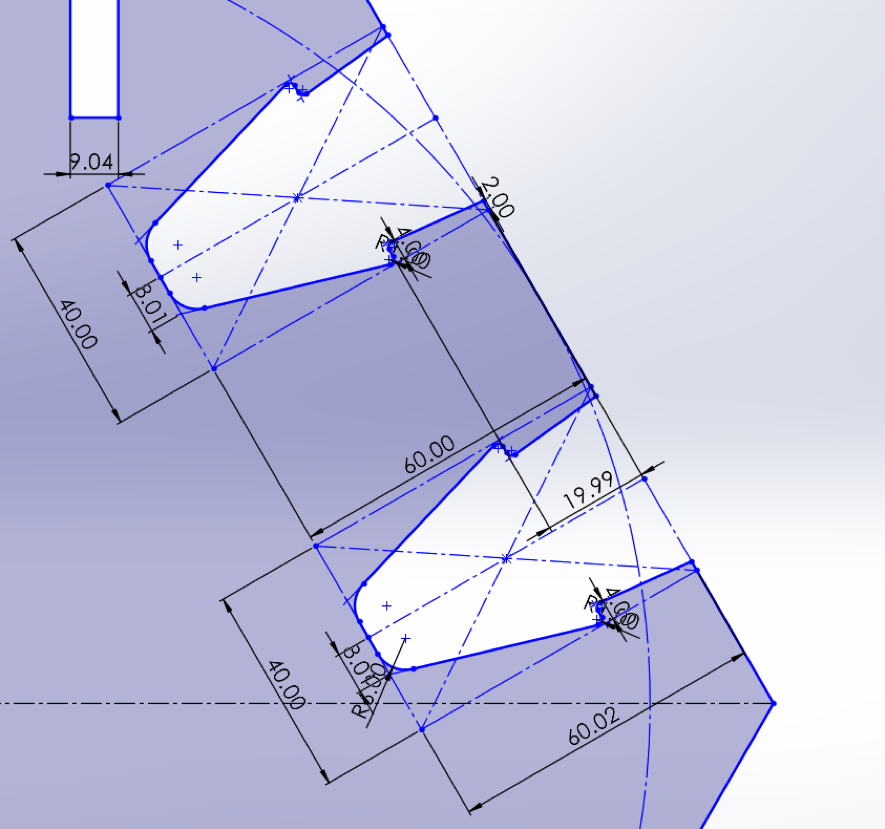
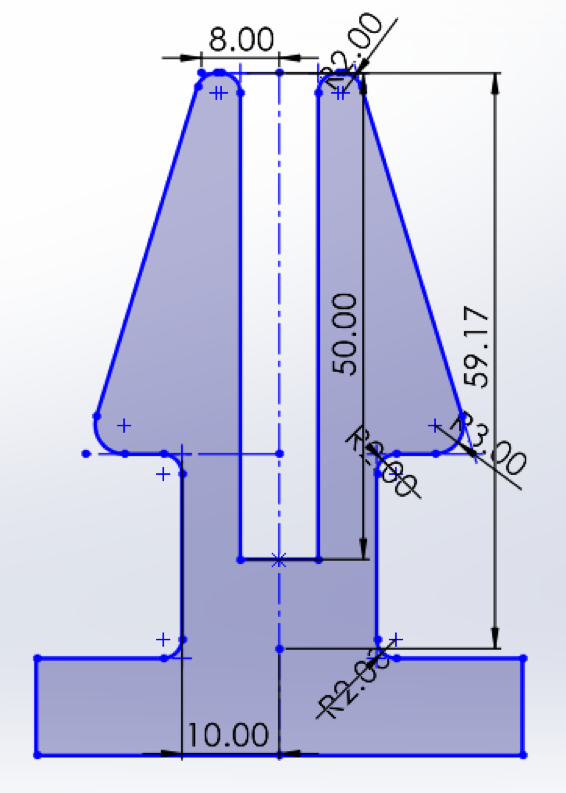
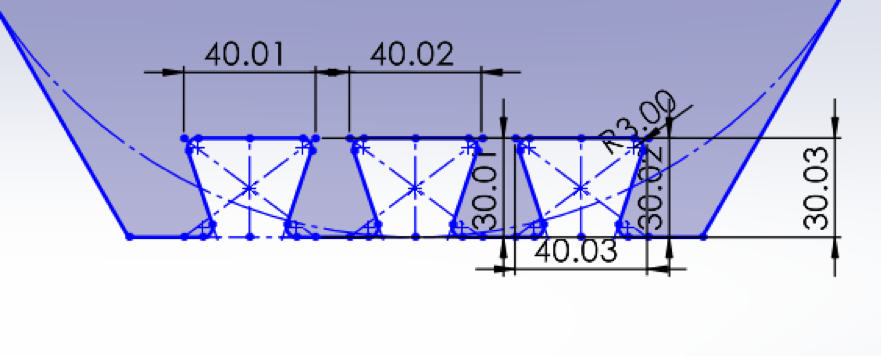
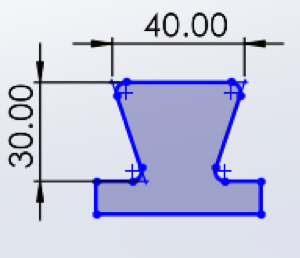
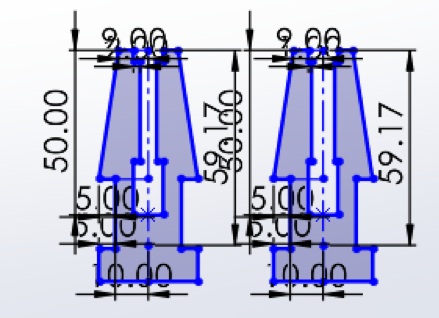
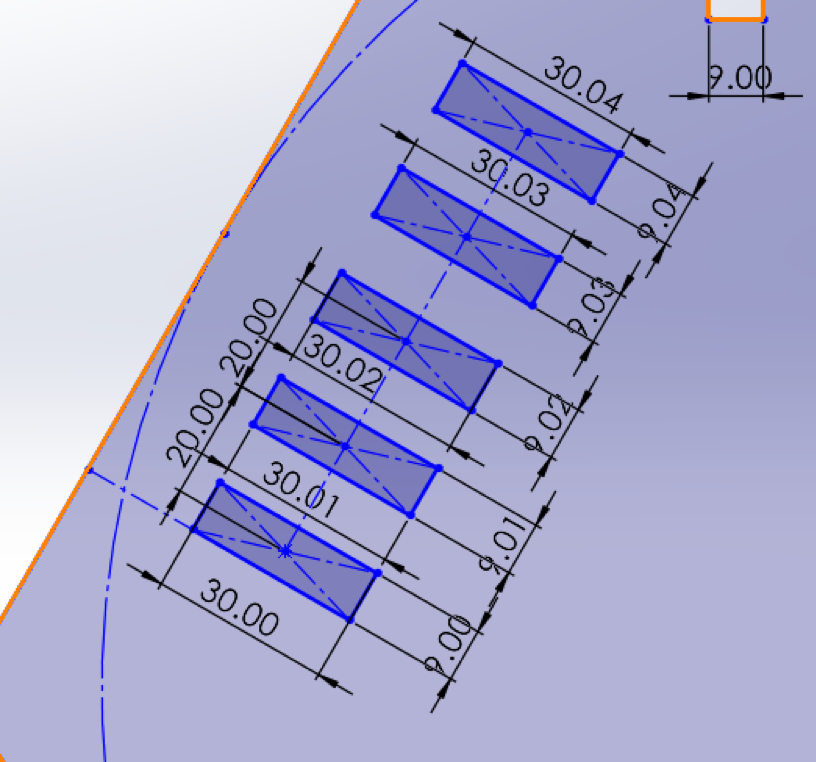
Once the design was ready, we ran a test cut on scrap material to make sure everything was perfect. Then, we watched as the CNC machine did its magic, carefully cutting each piece.
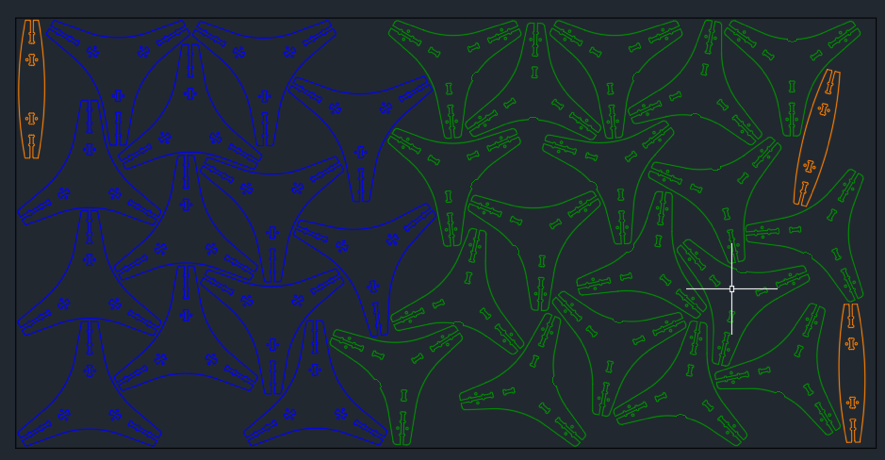
5. The Big Moment: Assembly
After cutting all the pieces, it was time to put them together. No screws, no glue – just pure precision. We sanded the edges to remove splinters, then started assembling. It was a bit like solving a 3D puzzle, but in the end, we built a structure that was sturdy and stable: the Latin American Pavilion. Watching it take shape was incredibly satisfying!
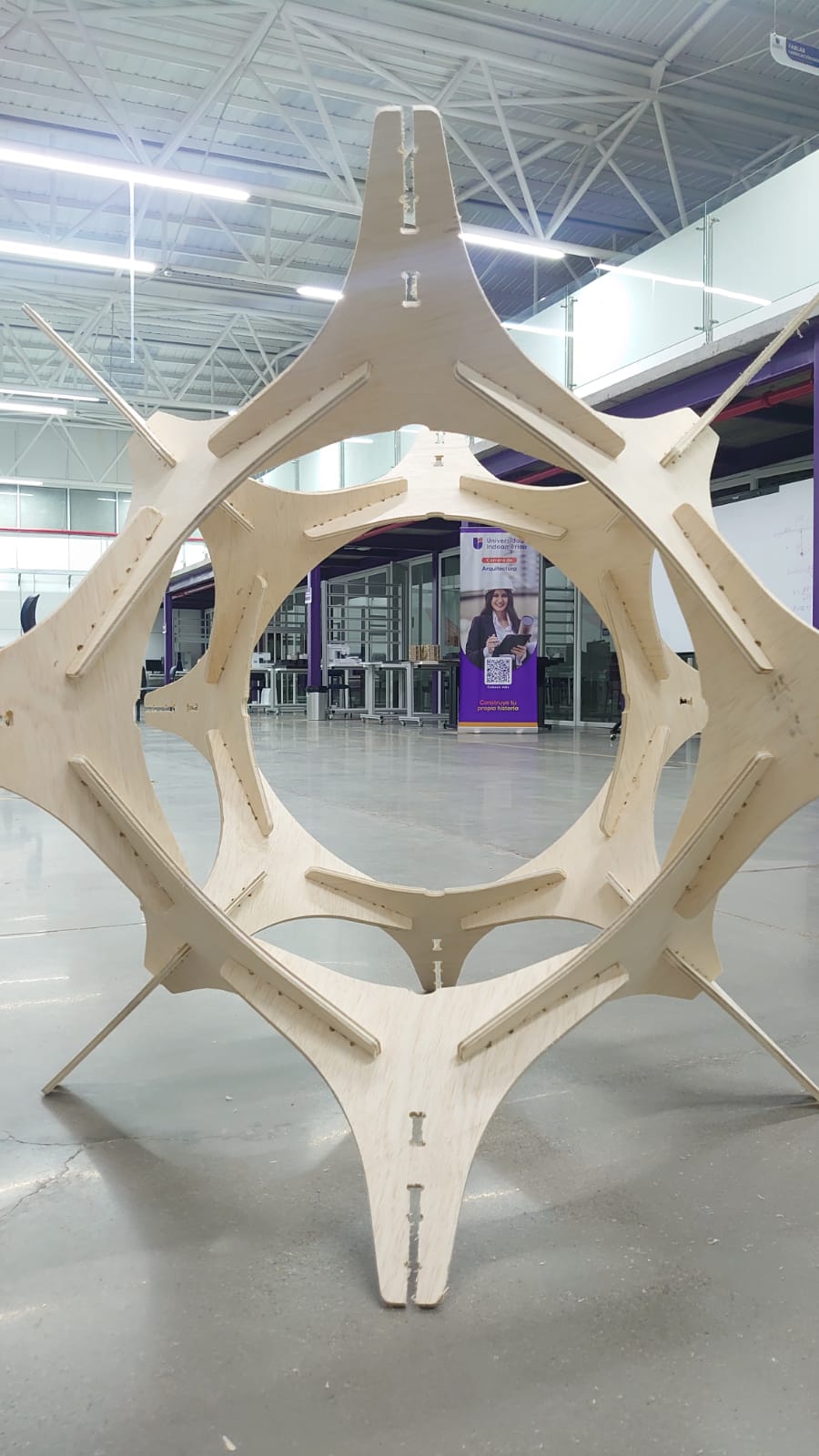
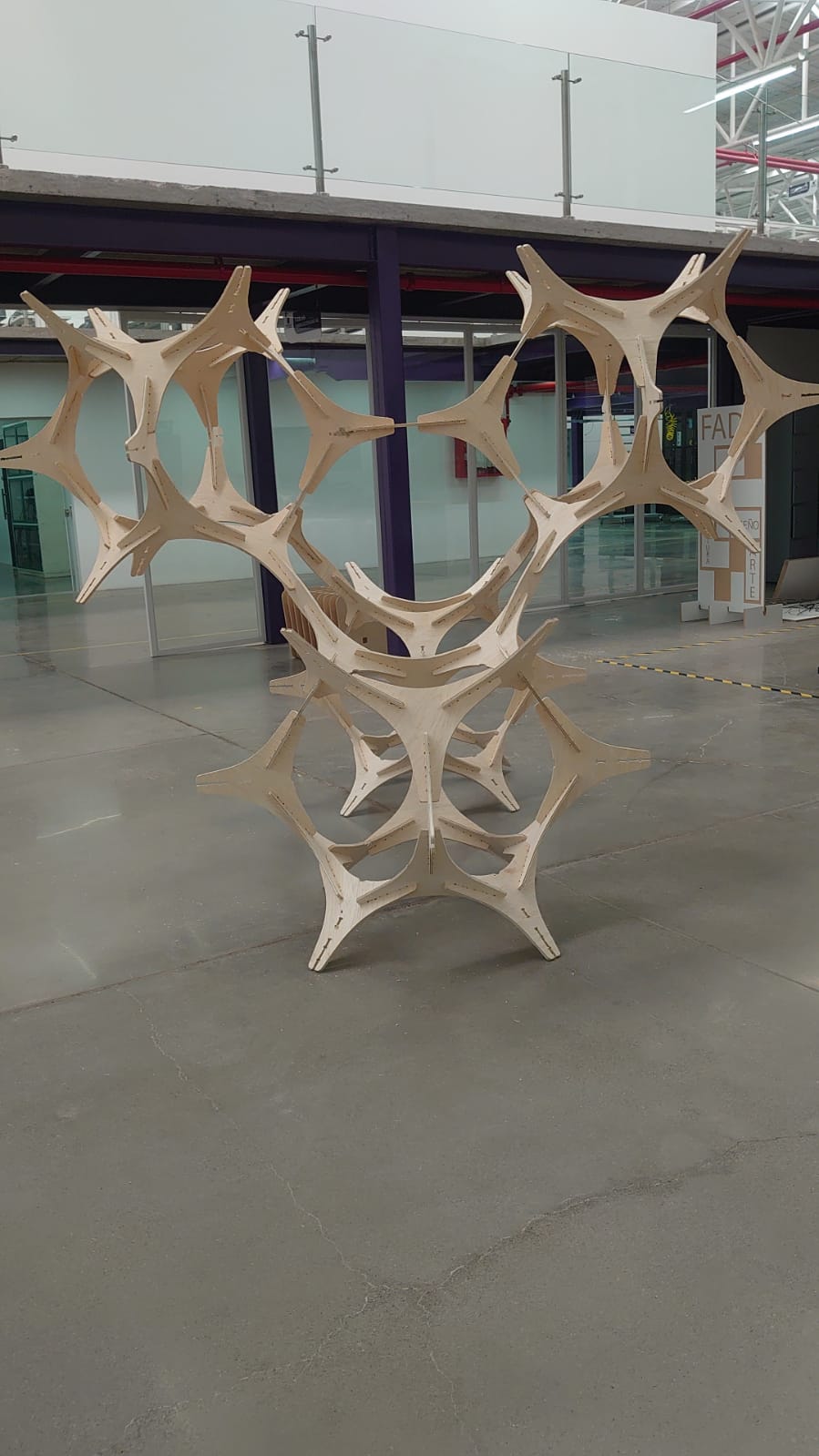
Lessons Learned
- Precision is everything – even a tiny misalignment can throw off the whole design.
- Choosing the right cutting parameters makes a huge difference in the final product.
- Press-fit joints, when designed correctly, are incredibly strong and don’t need glue.
- Patience and testing are key – rushing leads to mistakes.
Final Conclusions
It wasn't just a task, it was an experience. From designing the parts to watching the CNC machine bring them to life, every step was practical and rewarding. And the best part? Knowing that we have built something solid with clever design and good craftsmanship.
Individual Practice
Extra Credit: No fasteners or glue used, includes curved surfaces.
1. Design / Modeling of the Furniture/Bookcase
For the design of the furniture (bookcase), SolidWorks was used. We started from a basic design of 4 pieces, integrated with the previously tested press-fit assemblies.
For its bases, we used a common assembly where, by means of pressure, its structure and a rib (which serves as support for the pieces that will hold the books) were articulated to the base.
In the first pieces, they are simple models that integrate the design.
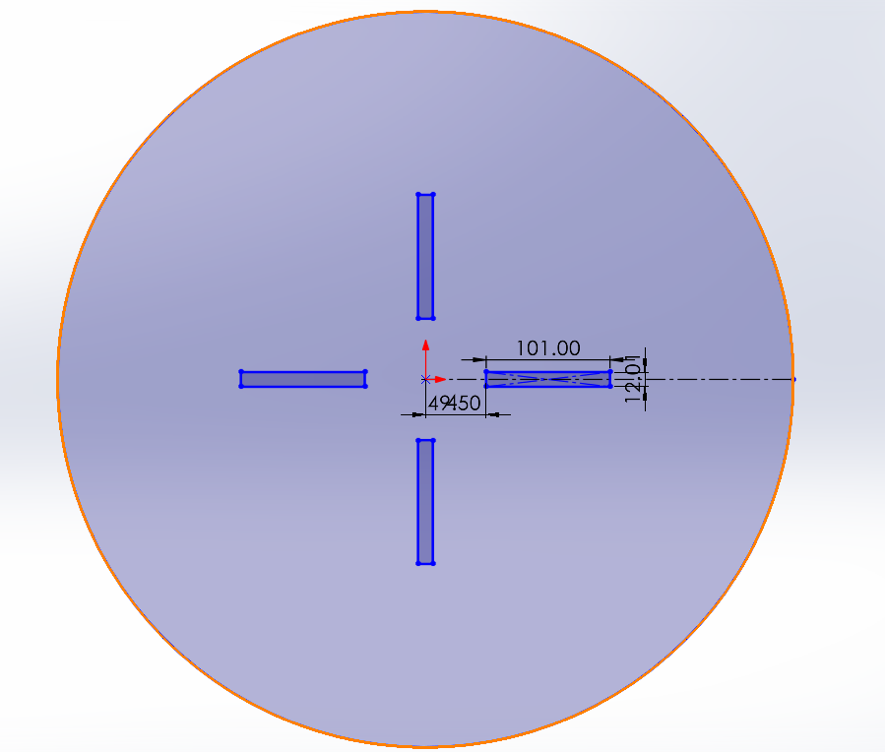
The Design Considers a Circular Base or Support
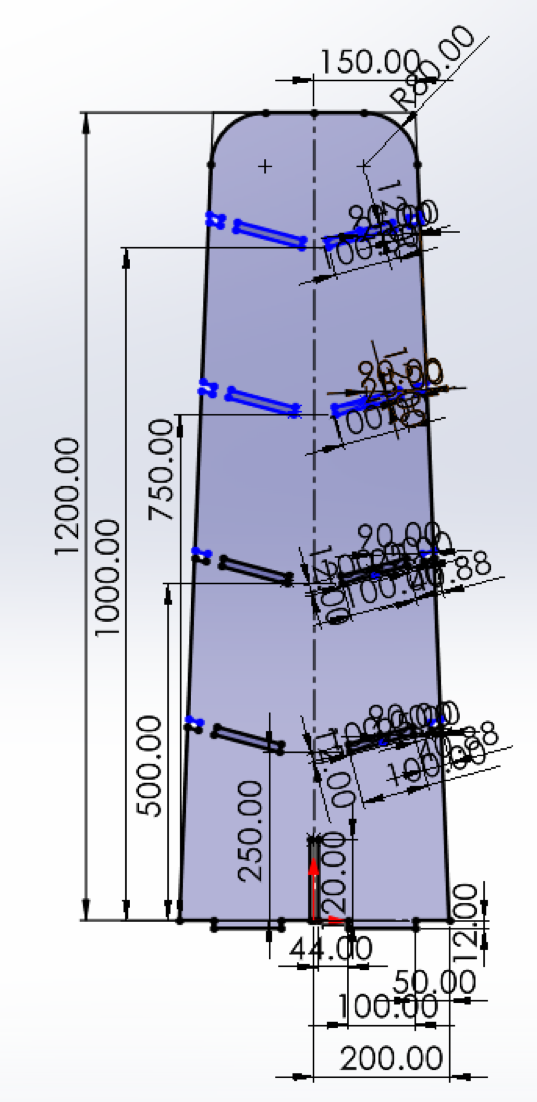
Design of Support Rib for Structure
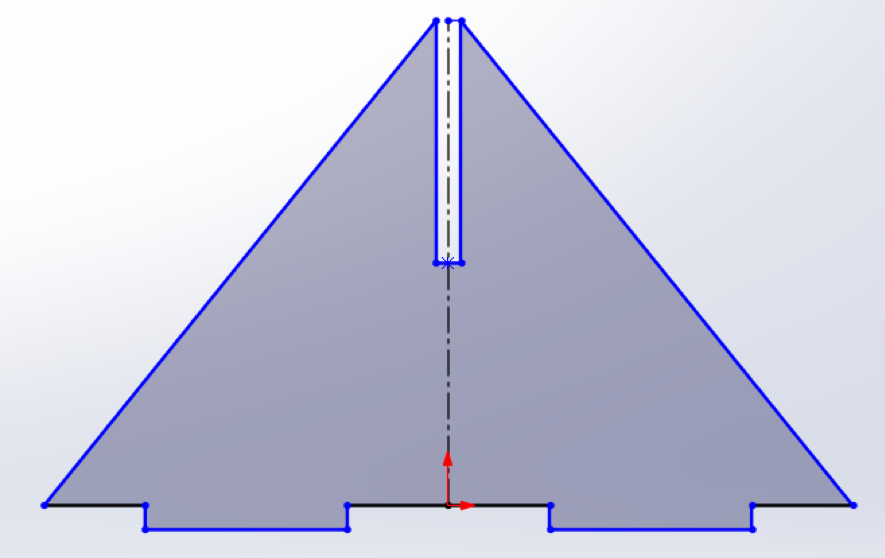
Book Supports with Reinforced Press-Fit Joints
For the book supports, we used the latest design made on the press fittings, as this structure will have to support the weight of the books.
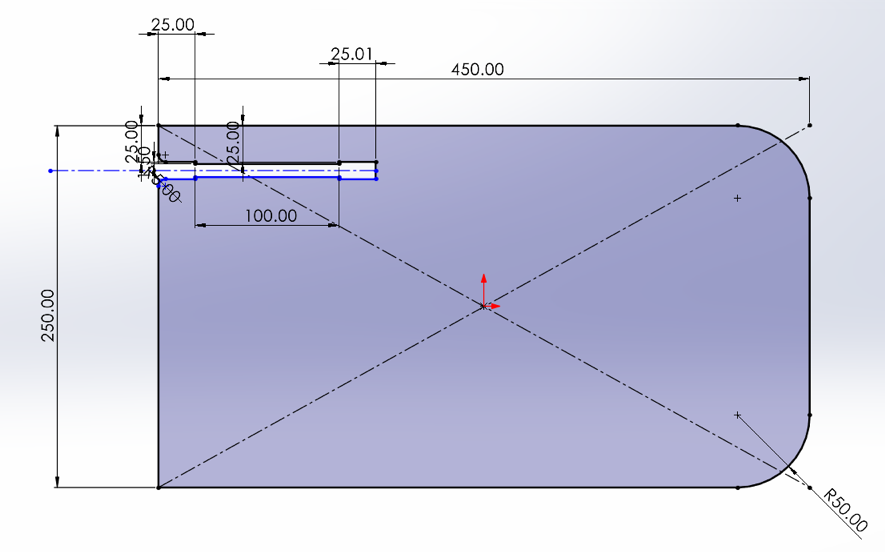
Assembly Simulation
After designing all the parts, we carried out a simulation of assemblies to determine their correct functioning.
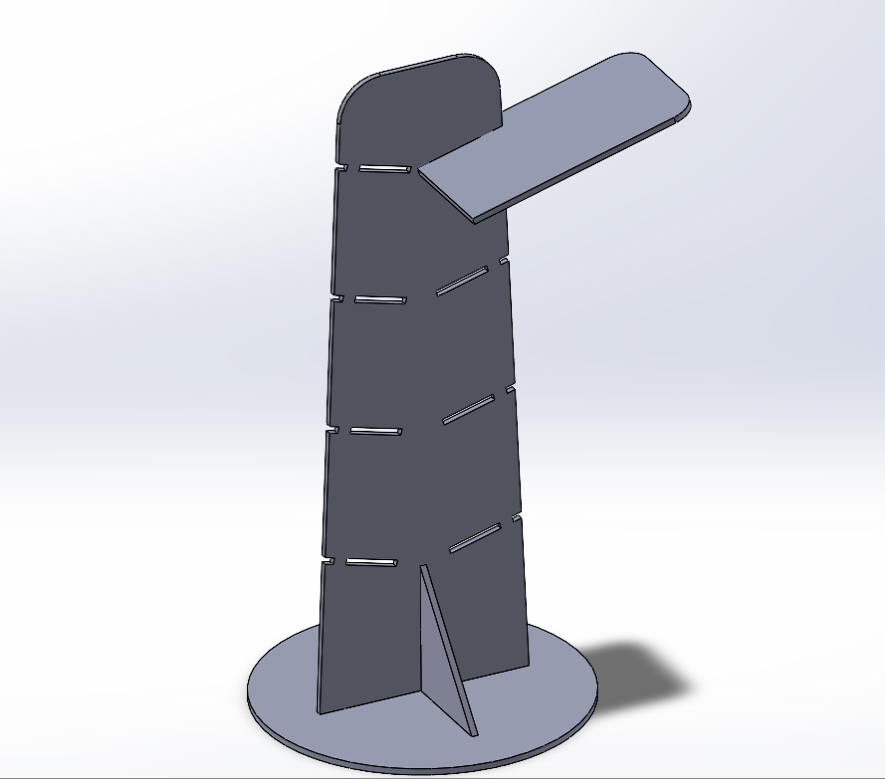
Transfer to DXF and Machine Configuration
As the next step, we transferred the files in DXF format to the program where we configured the files for cutting.
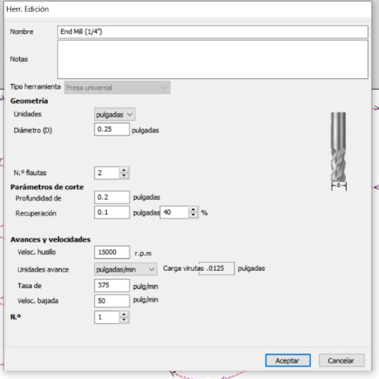
First, we configured the tool.
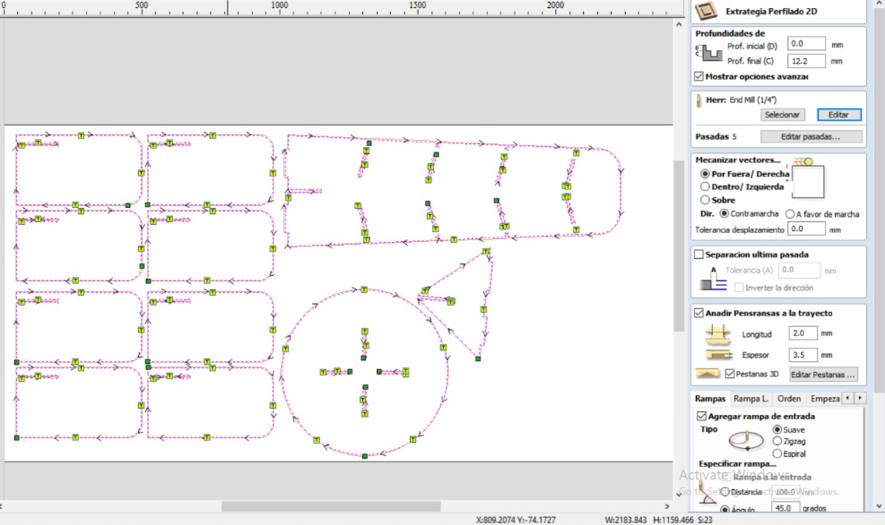
As a next step, we selected the lines of the files on which we were going to cut, as well as the configuration parameters of the machines we were going to use.
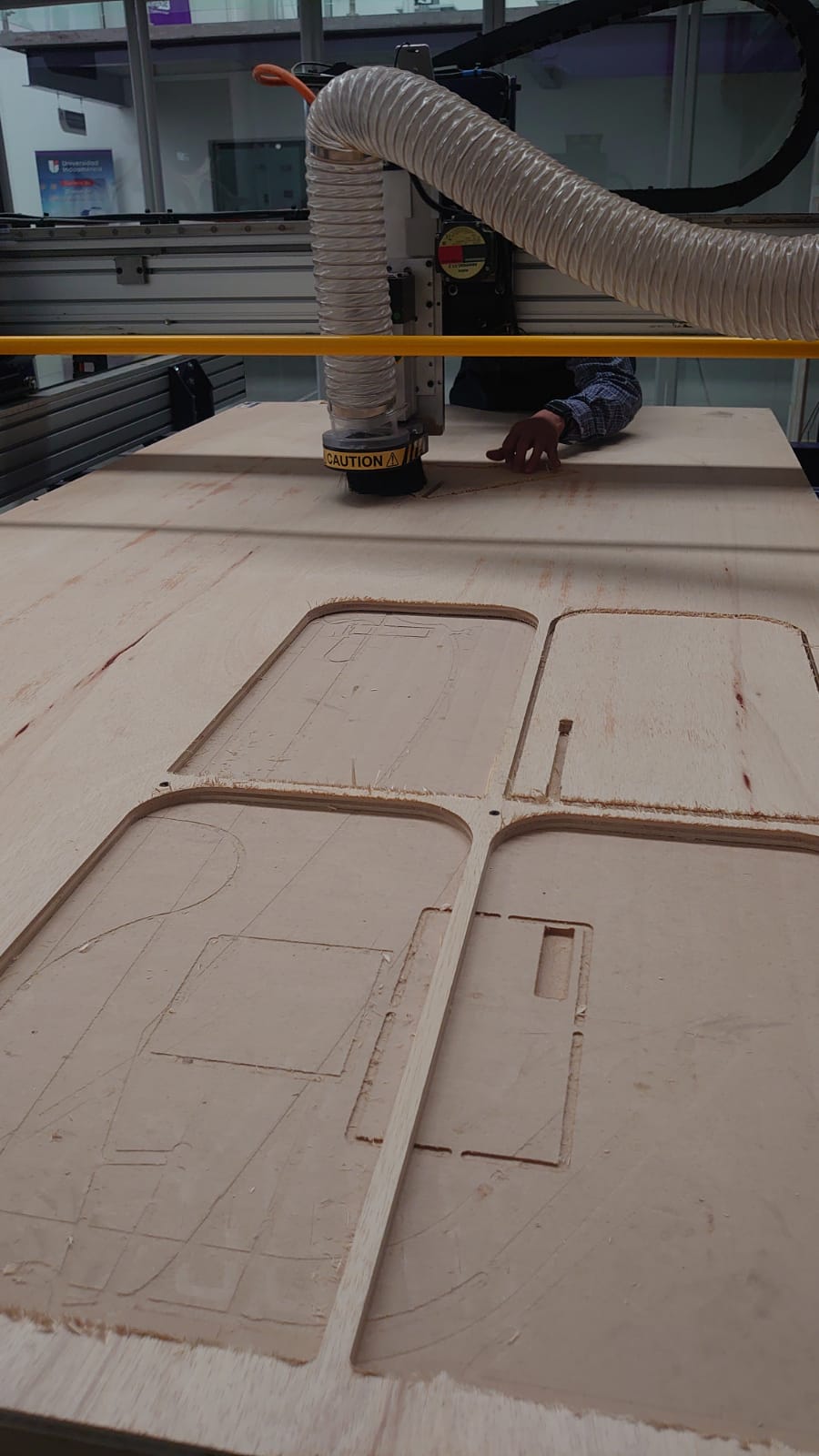
Once the configuration was done, we made the cut on the machine for the actual assembly.
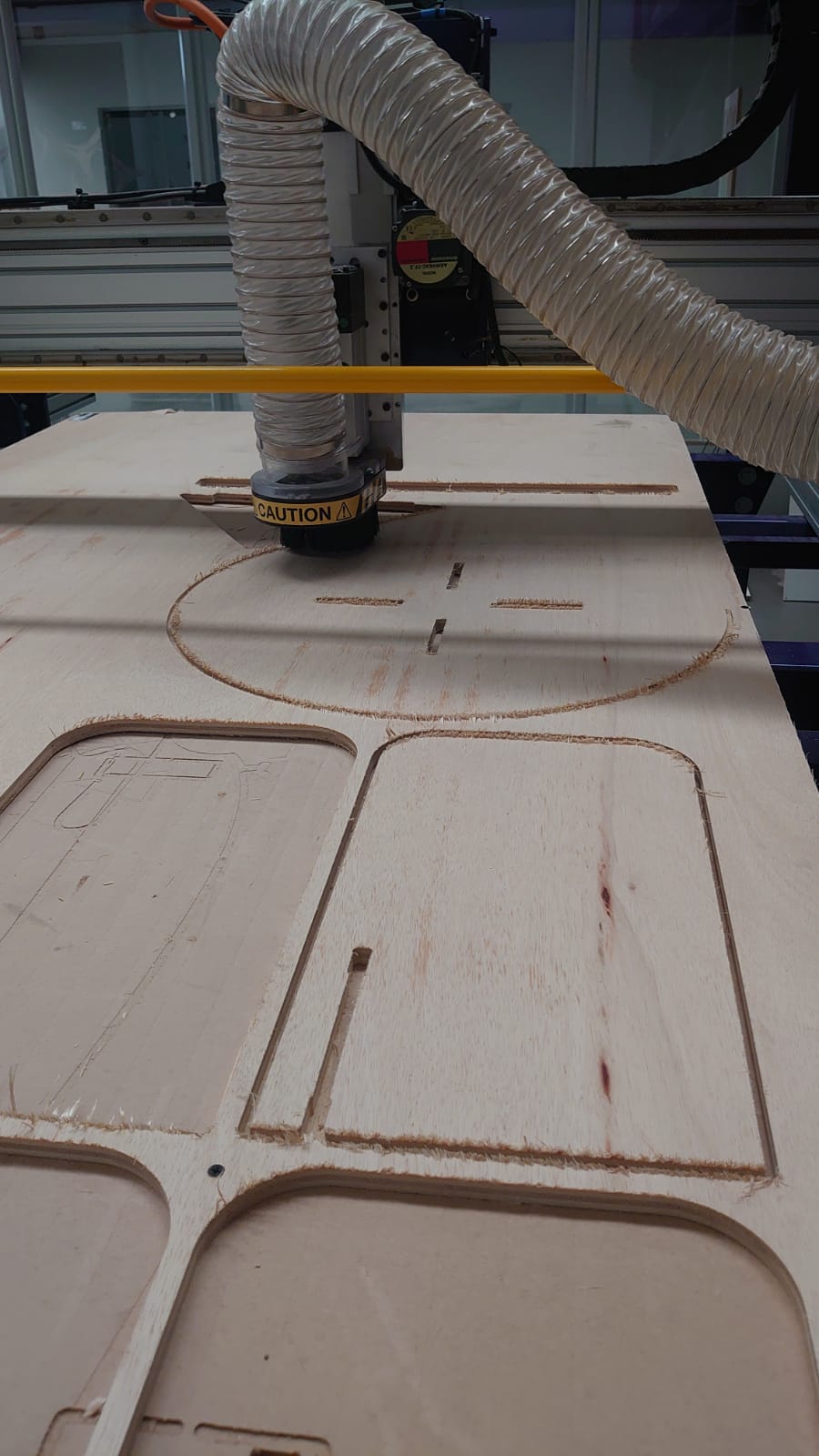
Cutting Process
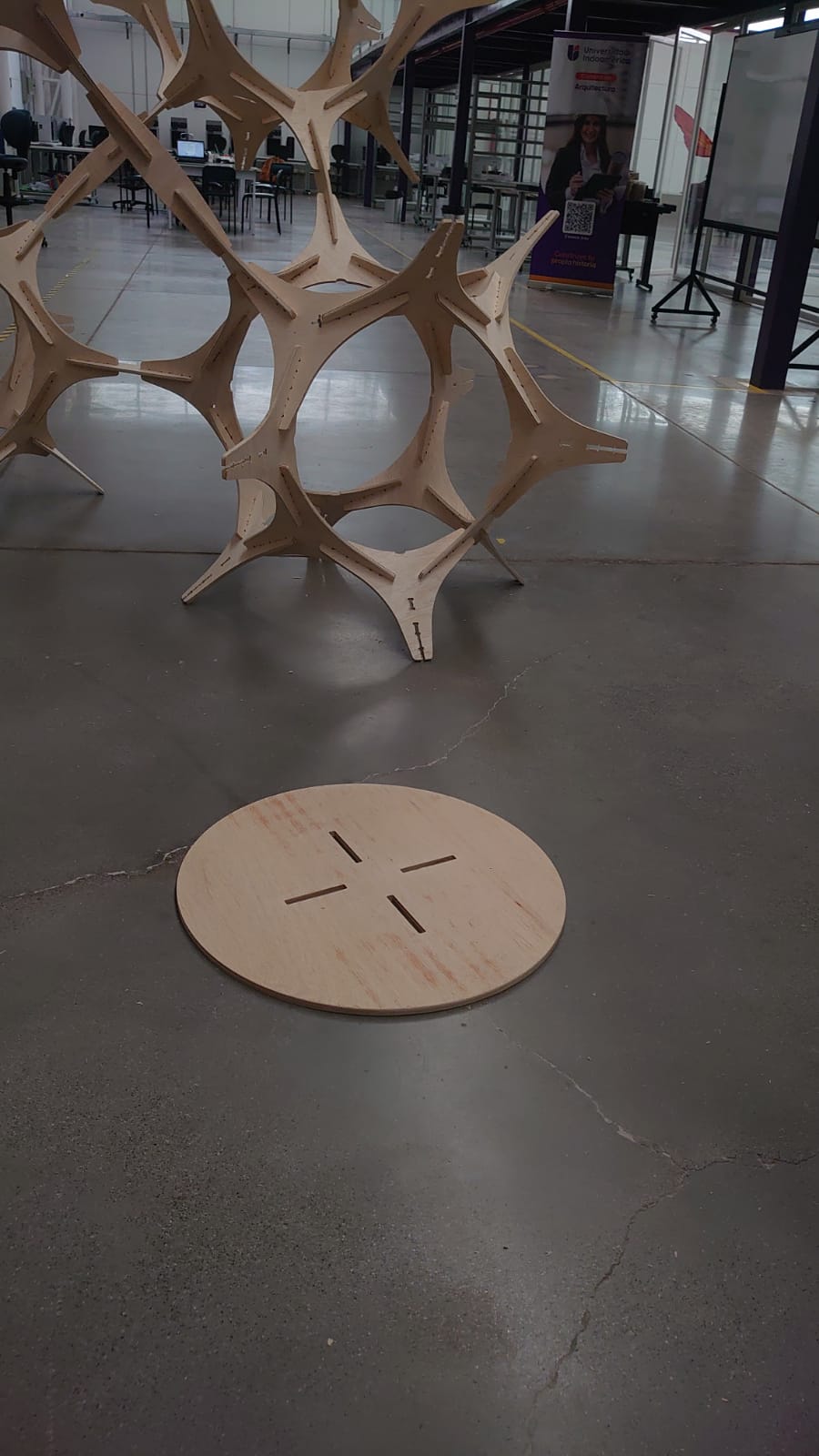
Sanding and Assembly
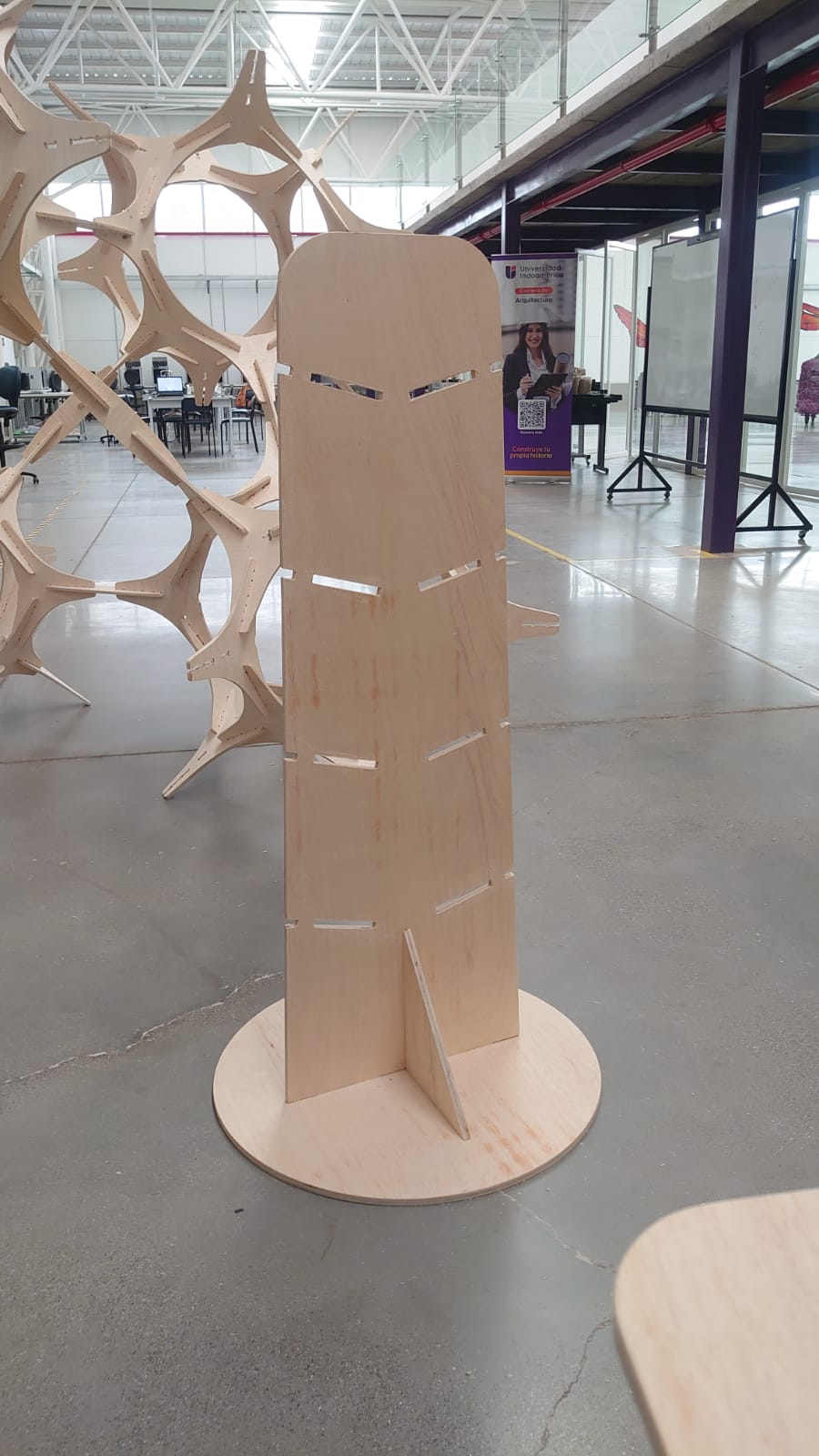
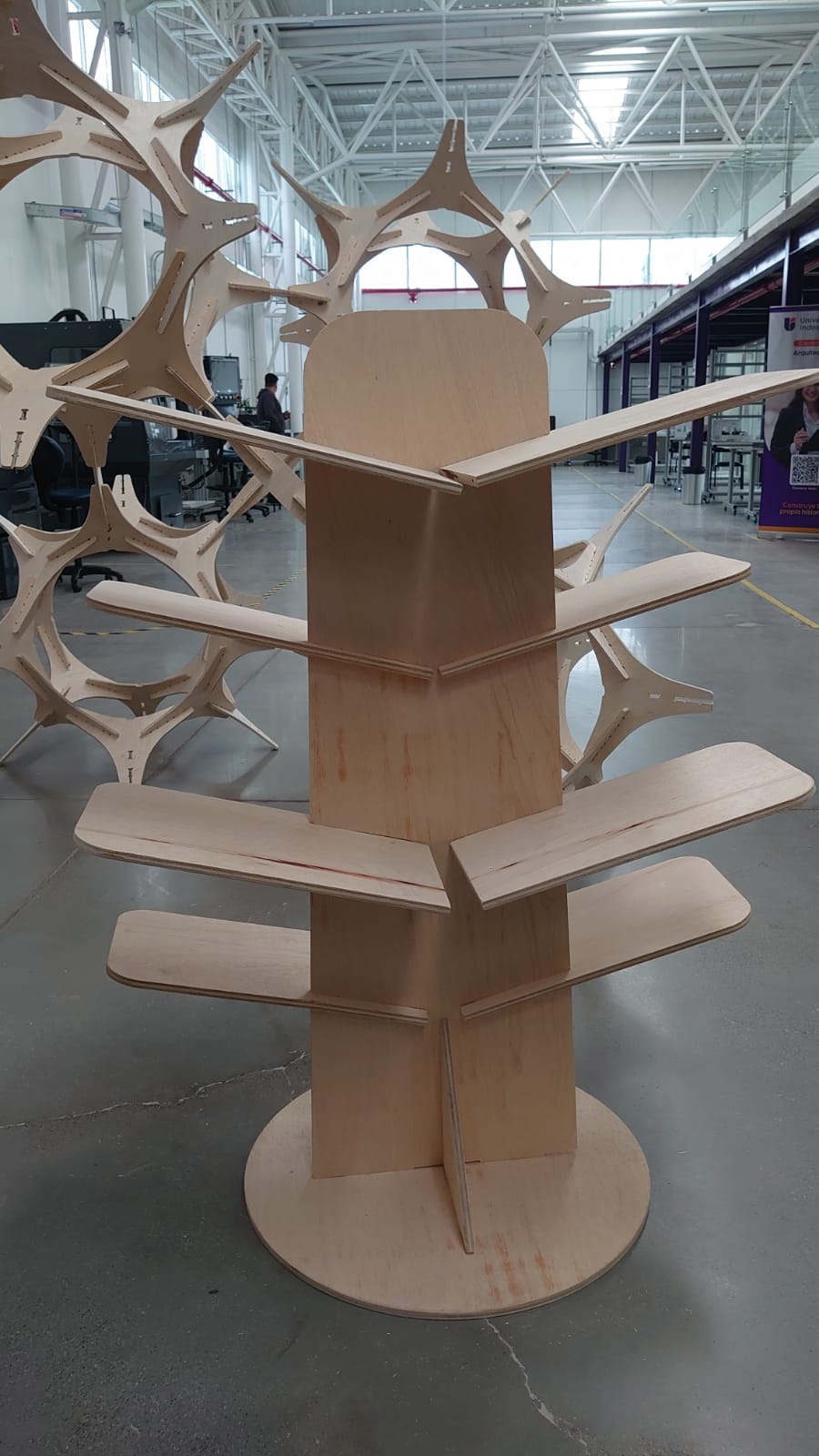
Furniture in Use

Final Conclusions
This week's assignment focused on the process of designing, cutting, and assembling a functional object using CNC machining. The experience was very interesting as it reinforced the importance of projecting functionality and, at the same time, materializing it.
Key Takeaways
- Safety protocols ensure a secure workflow.
- Machine calibration is critical for precision.
- Tool path optimization enhances efficiency and quality.
- Each step contributes to a coherent construction.